In the age before electricity powered our factories and machines, early mills relied on water and steam to drive production. Water-powered and steam-powered mills were the engines of industry, providing the energy needed to power machinery for everything from grinding grain to weaving fabric. Yet, the mechanisms that made these mills work were a far cry from today’s sophisticated systems. Among these, one unassuming but vital tool played a crucial role in the safe and efficient operation of early mills: the slip bearing.
The Mechanics of Water and Steam Powered Mills

Early water and steam-powered mills were marvels of mechanical engineering, relying on an intricate network of spinning shafts, gears, and pulleys. Without electricity, mills had to transfer power generated from water wheels or steam engines directly to the machinery. To accomplish this, they used a series of spinning shafts that ran throughout the mill. These shafts, supported by a system of hanger rods attached to the ceiling, transmitted energy to various parts of the building.
However, transferring power through these rotating shafts required robust and durable components, particularly where the shafts connected with their support structures. At these critical junctions, slip bearings played a central role. Let’s delve deeper into what these bearings were and why they mattered so much in these early industrial settings.
What is a Slip Bearing?
Slip bearings, also known as plain bearings, were a type of bearing that allowed shafts to spin smoothly by reducing friction between moving parts. Unlike modern bearings, which often use rolling elements like balls or rollers, slip bearings consist of two surfaces that slide against each other. In early mills, these bearings were made from a soft metal alloy, often referred to as bearing metal, which was designed to be less durable than the shaft it supported. This way, any wear or damage would occur to the bearing rather than the shaft.
1. How Slip Bearings Worked
Slip bearings worked by providing a smooth surface for the shaft to rotate within the hanger rod support. When properly lubricated, the friction between the shaft and the bearing was minimized, allowing for continuous movement. This lubrication, typically oil or grease, was essential to prevent excessive wear and overheating.
2. The Importance of Lubrication
Lubrication was the lifeblood of these bearings. Without a steady supply of oil or grease, the friction between the shaft and bearing would cause extreme heat. Given enough time, this heat could even cause the bearing metal to soften, deform, or melt. This risk meant that maintaining lubrication was a constant priority for mill workers, as it prevented costly breakdowns and ensured the safety of the operation.
The Tool for Catching Oil and Grease: A Forgotten Hero of Early Industry
To keep slip bearings properly lubricated, early mills used a simple but essential tool to catch the oil or grease that would drip from these bearings. This tool, which might seem insignificant by today’s standards, played a vital role in the daily operation of mills. Essentially, it was designed to catch any excess lubrication that dripped from the bearings, ensuring that the machinery stayed greased and that flammable oil didn’t accumulate on the mill floor—a critical feature in an era when most mills were constructed from wood.
1. Preventing Disaster with a Simple Tool
The oil and grease-catching tool did more than just protect the floor from stains. In the bustling environment of a mill, the buildup of grease or oil on wooden surfaces presented a real fire hazard. By catching these drips, the tool reduced the risk of fires, which could quickly spread through a mill’s wooden structure, endangering workers and destroying valuable equipment.
2. Reducing Maintenance and Downtime
By catching excess grease, this tool also reduced maintenance demands on mill workers. It allowed them to easily access and recycle lubricants if needed, helping to maintain efficient operation and minimize downtime. Without these catchers, mills would have faced greater difficulties with lubrication management, potentially leading to more frequent failures and interruptions in production.
The Consequences of Running Out of Grease
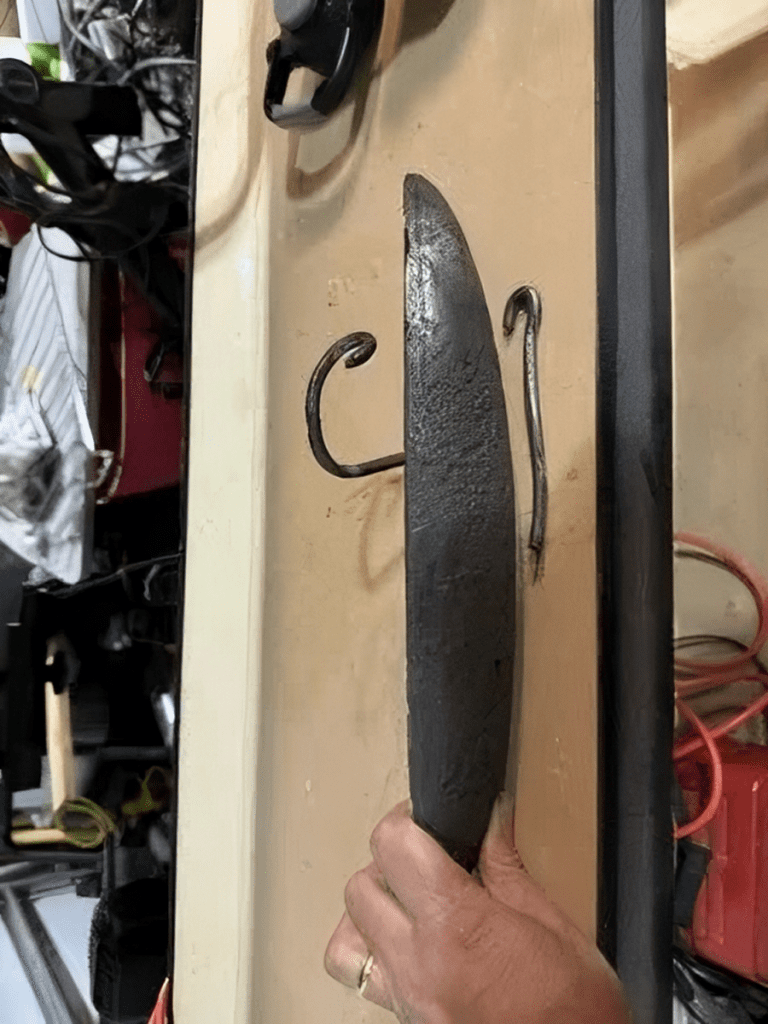
What happened when slip bearings ran out of grease? The results could be catastrophic. Without lubrication, friction would rapidly build up, causing the bearing metal to reach high temperatures. In extreme cases, the metal would begin to melt. This molten metal could drip from the ceiling, not only presenting a serious safety hazard to workers below but also increasing the risk of fire.
1. The Danger of Fire in Early Mills
Wooden mills, combined with hot, friction-prone machinery, created an environment ripe for fires. If bearings overheated, the combination of molten metal and oil residue could ignite the structure, leading to devastating fires. For this reason, maintaining proper lubrication was not only a matter of functionality but also a matter of safety.
2. Avoiding Costly Repairs
A melted bearing could cause extensive damage to both the shaft and the hanger rods, requiring significant repairs or replacements. Since early mills did not have the convenience of ordering replacement parts quickly, a major failure could halt operations for days or even weeks. The importance of keeping these bearings lubricated, therefore, extended to both the safety of workers and the economic health of the mill.
Slip Bearings: A Testament to Industrial Innovation
While simple, slip bearings and their associated maintenance tools were vital to the operation of early mills. They represented the ingenuity of a time when industrial innovation was driven by practical solutions rather than advanced technology. These bearings and their lubrication tools remind us that the success of early industry was built on the back of functional, reliable equipment.
1. A Legacy of Industrial Ingenuity
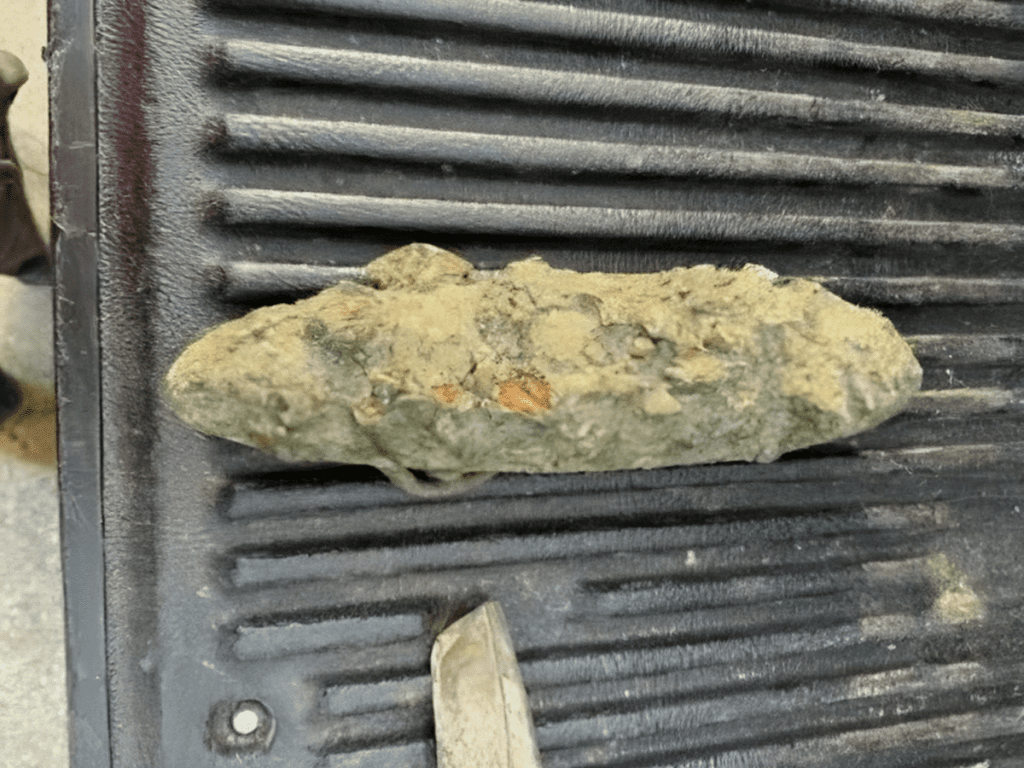
Slip bearings paved the way for future advancements in mechanical engineering. Their design, while basic, reflected the needs of an industry that relied on endurance and simplicity. As industries grew more complex, these early components evolved into the sophisticated bearing systems we see today.
2. How Modern Bearings Have Evolved
Modern bearings benefit from technological advances that minimize friction and improve longevity. Today, we use ball bearings, roller bearings, and other complex designs that were unimaginable in the age of water and steam-powered mills. Yet, the principles of reducing friction, ensuring durability, and maintaining safety remain central to industrial machinery.
Conclusion: Remembering the Forgotten Tools of Early Industry
The oil-catching tool and slip bearings used in water and steam-powered mills may seem like minor details in the grand scheme of industrial history. However, they played a crucial role in keeping early mills operational, safe, and efficient. These tools serve as reminders of a time when simple solutions and diligent maintenance kept the gears of industry turning.
By understanding these forgotten tools, we gain a deeper appreciation for the ingenuity and resourcefulness that drove the early industrial revolution. It’s easy to take today’s technology for granted, but it’s worth remembering that every modern advancement stands on the foundation built by these early innovations. The next time you see a sleek, modern machine, remember the humble slip bearing and the role it played in shaping the future of industry.